Industrial Perforated Metal Sheets for Custom Fabrication
Browse high-quality industrial perforated metal sheets ideal for filtration, ventilation, and architectural use.
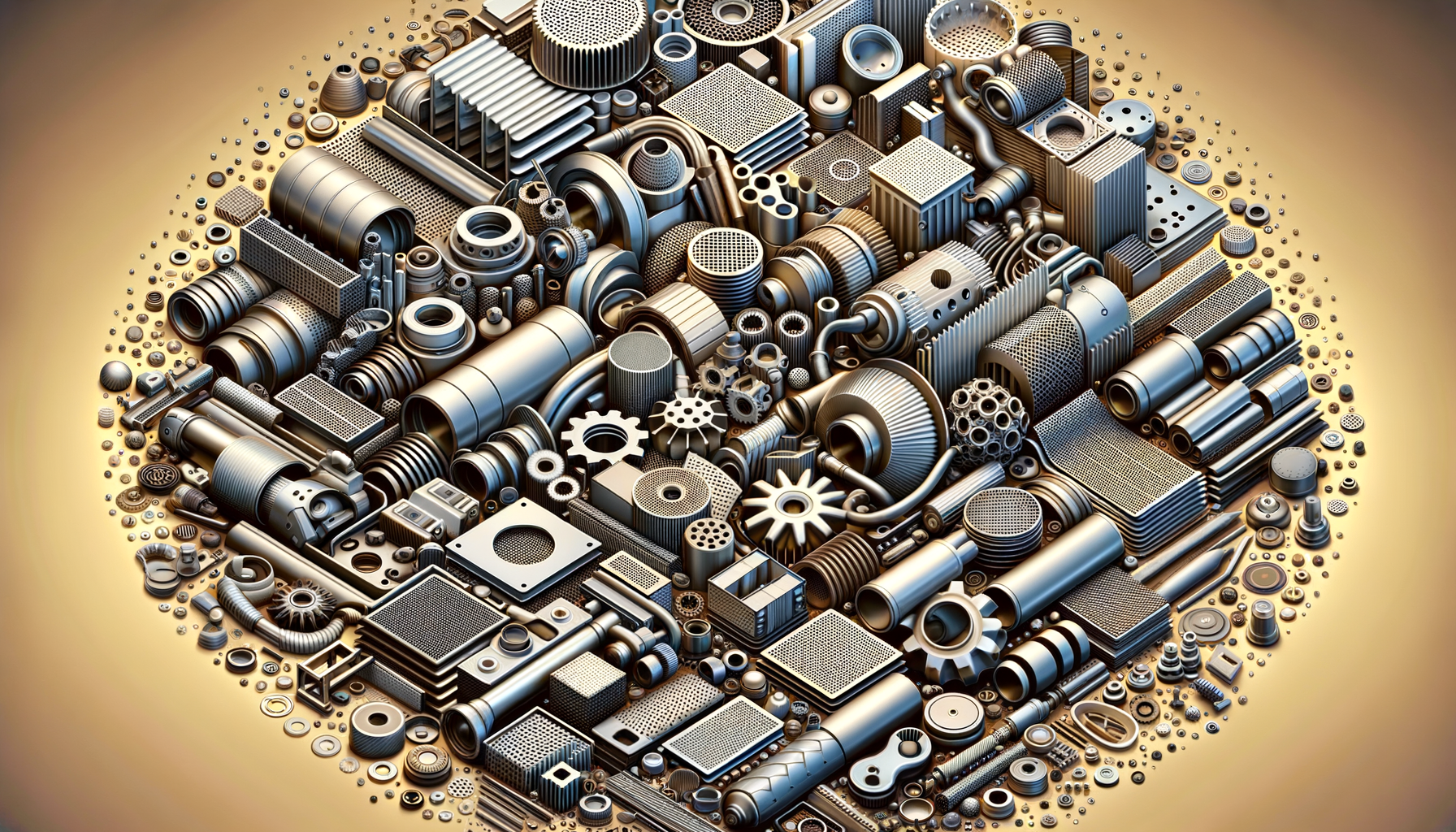
Introduction to Industrial Perforated Metal
Industrial perforated metal sheets are a versatile and essential component in various sectors, offering a combination of functionality and aesthetic appeal. These sheets are crafted by punching holes into metal surfaces, which can be customized to meet specific requirements. Their significance spans across industries, from filtration and ventilation to architectural enhancements, making them an invaluable asset in both practical and decorative applications.
Perforated metal sheets are particularly renowned for their ability to provide solutions in environments where airflow, light, and sound control are critical. The perforations allow for efficient passage of air and light, while also serving as a sound barrier. This unique combination of properties makes them ideal for use in HVAC systems, noise control applications, and even artistic installations. As industries continue to evolve, the demand for high-quality industrial perforated metal sheets remains robust, underscoring their importance in modern fabrication.
Applications of Perforated Metal Sheets
The applications of perforated metal sheets are as diverse as the industries they serve. One of the primary uses is in filtration systems, where the perforations allow for the separation of solids from liquids or gases. This is particularly useful in chemical processing, food and beverage production, and water treatment facilities. The ability to customize the size and pattern of the perforations ensures that the sheets can be tailored to specific filtration needs.
In addition to filtration, perforated metal sheets are extensively used in ventilation systems. The perforations facilitate the flow of air, making them ideal for use in HVAC systems, industrial exhausts, and even kitchen ventilation hoods. Their lightweight nature and strength make them easy to install and maintain, providing long-lasting performance in demanding environments.
Architecturally, perforated metal sheets are employed to enhance the aesthetic appeal of buildings. They can be used as facades, sunshades, and decorative panels, offering a modern and sleek look. The ability to create intricate designs through perforation allows architects to experiment with light and shadow, adding a dynamic element to building exteriors.
Material Choices for Perforated Metal
The choice of material for perforated metal sheets significantly impacts their performance and suitability for specific applications. Common materials include stainless steel, aluminum, and mild steel, each offering distinct advantages. Stainless steel is known for its corrosion resistance and durability, making it ideal for outdoor and harsh environments. Aluminum, being lightweight and resistant to corrosion, is preferred in applications where weight is a critical factor, such as in aerospace and automotive industries.
Mild steel, on the other hand, is favored for its strength and cost-effectiveness, making it suitable for structural applications. The selection of material also influences the aesthetic qualities of the perforated sheets. For instance, aluminum can be anodized to achieve a variety of colors, while stainless steel can be polished for a high-gloss finish. This versatility in material choice allows for customization to meet both functional and aesthetic requirements.
Moreover, the thickness of the metal sheets can be adjusted according to the intended use, providing flexibility in design and application. Thicker sheets offer enhanced strength and durability, while thinner sheets are easier to work with and install. This adaptability makes perforated metal sheets a preferred choice across a wide range of industries.
Customization and Design Considerations
Customization is a key feature of industrial perforated metal sheets, allowing them to be tailored to specific project needs. The pattern, size, and shape of the perforations can be adjusted to achieve desired outcomes, whether it’s for functional or decorative purposes. Common perforation patterns include round, square, and slotted holes, each offering different properties in terms of airflow, light transmission, and strength.
Design considerations also extend to the spacing and arrangement of the perforations. Closely spaced holes can enhance sound absorption and provide a more uniform appearance, while wider spacing can increase airflow and reduce material usage. These design elements are critical in applications such as acoustic panels, where sound control is paramount, and in architectural facades, where visual impact is a priority.
The customization process often involves advanced manufacturing techniques such as CNC punching and laser cutting, which ensure precision and consistency in the perforation patterns. This level of detail allows for the creation of intricate designs that can transform simple metal sheets into stunning architectural features or highly efficient industrial components.
Conclusion: The Future of Perforated Metal Sheets
The future of industrial perforated metal sheets looks promising as industries continue to seek innovative solutions for complex challenges. The ability to combine functionality with aesthetic appeal makes these sheets a valuable asset in both traditional and emerging markets. As technology advances, the potential for even more sophisticated customization and application of perforated metal sheets will likely expand, offering new opportunities for innovation in design and engineering.
For businesses and industries looking to enhance their operations or architectural designs, investing in high-quality perforated metal sheets is a strategic move. With their proven track record in diverse applications, these sheets are set to remain a staple in industrial and architectural fabrication for years to come.