Industrial Thermography Services: Detect Issues Before They Escalate
Thermography services use infrared imaging to detect hidden faults in equipment, helping industries prevent failures and reduce downtime.
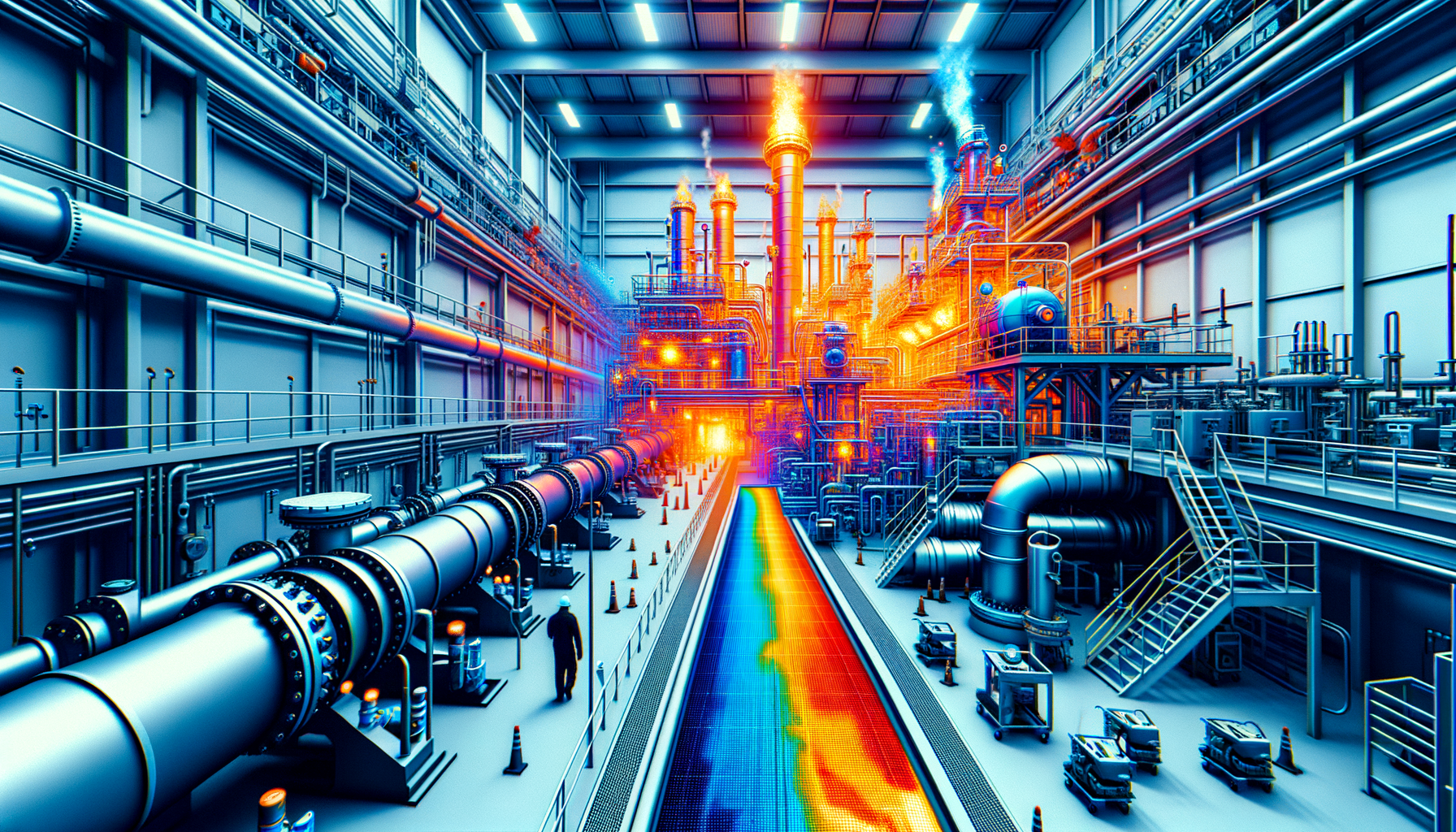
Introduction to Industrial Thermography
Industrial thermography has emerged as a crucial tool in predictive maintenance, helping industries to avert potential failures before they occur. By using infrared imaging, industrial thermography services can detect anomalies in equipment that are invisible to the naked eye. These anomalies often signify underlying issues that, if left unchecked, could lead to significant downtime and costly repairs. This technology is not only about identifying current problems but also about preventing future failures, thereby enhancing operational efficiency and safety.
The Science Behind Thermography
Thermography operates on the principle of infrared radiation. All objects emit infrared radiation as a function of their temperature. Thermographic cameras detect this radiation and convert it into a visible image, known as a thermogram. The thermogram displays temperature variations, which are crucial for identifying potential issues in industrial equipment. For instance, a hotspot in a thermogram might indicate excessive friction or electrical resistance, both of which could lead to equipment failure. By interpreting these images, technicians can pinpoint areas that require maintenance, thus preventing costly downtime.
Applications in Various Industries
Industrial thermography finds applications across a wide range of industries, each benefiting from its ability to detect issues early. In the electrical industry, for instance, thermography is used to inspect electrical panels and connections. A rise in temperature in these areas can indicate loose connections or overloaded circuits, which, if not addressed, could lead to fires. Similarly, in the mechanical industry, thermography helps in monitoring the condition of bearings and motors. By identifying abnormal heat patterns, maintenance teams can address issues before they escalate into major failures. This proactive approach not only saves money but also enhances safety and reliability.
Benefits of Implementing Thermography
The implementation of thermography in industrial settings offers numerous benefits. Firstly, it is a non-invasive and non-destructive method, meaning that inspections can be carried out without interrupting operations. This is particularly advantageous in industries where downtime can be extremely costly. Secondly, thermography provides immediate results, allowing for quick decision-making. Thirdly, it enhances safety by identifying potential hazards before they manifest. Furthermore, by integrating thermography into regular maintenance schedules, industries can extend the lifespan of their equipment and reduce the likelihood of unexpected failures.
Future Trends in Industrial Thermography
As technology advances, the field of industrial thermography is poised for significant growth and innovation. One emerging trend is the integration of thermography with other technologies, such as drones and artificial intelligence. Drones equipped with thermographic cameras can inspect hard-to-reach areas, such as tall structures or remote installations, with ease. Meanwhile, artificial intelligence can enhance the analysis of thermographic data, providing more accurate and predictive diagnostics. These advancements will further solidify thermography’s role as a vital component of industrial maintenance strategies, ensuring even greater efficiency and safety in the future.