Top Finned Double Pipe Heat Exchangers for Efficient Thermal Transfer
Compare efficient finned double pipe heat exchangers built for industrial cooling and heating. Explore cost-effective options designed for high performance and long-term reliability.
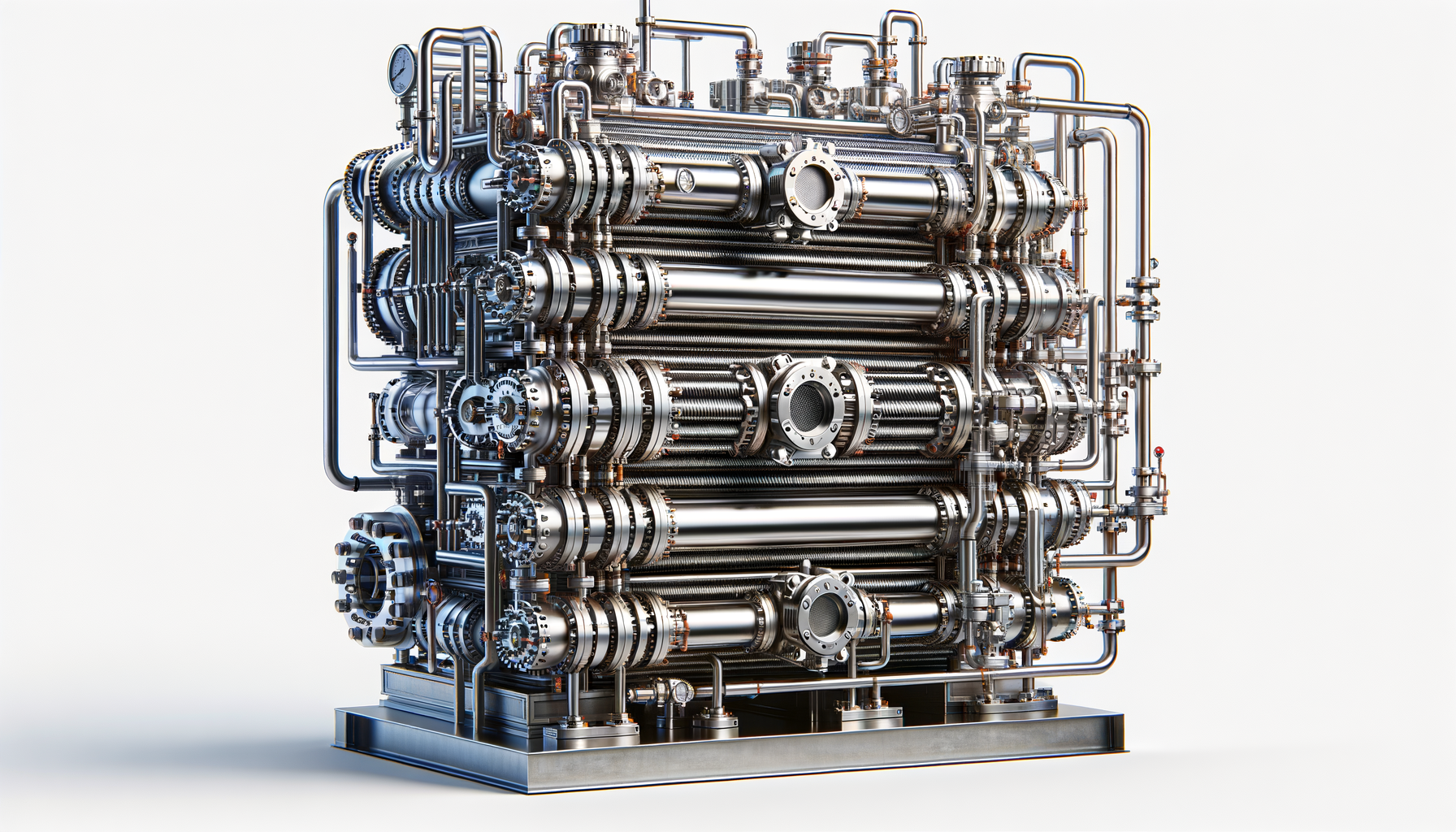
Introduction to Finned Double Pipe Heat Exchangers
In the realm of industrial applications, the role of heat exchangers is pivotal for processes that require efficient thermal management. Among the various types of heat exchangers, finned double pipe heat exchangers stand out due to their design and operational efficiency. These systems are engineered to enhance heat transfer between two fluids, making them indispensable in industries such as chemical processing, power generation, and HVAC systems. The incorporation of fins amplifies the surface area, thereby optimizing the heat exchange process and ensuring effective thermal management in various industrial scenarios.
Design and Functionality
The design of a finned double pipe heat exchanger is both simple and ingenious. It consists of two concentric pipes with one fluid flowing through the inner pipe and the other fluid flowing in the opposite direction through the annular space between the pipes. The fins attached to the outer surface of the inner pipe increase the heat transfer surface area, which is crucial for enhancing the efficiency of the exchanger. This design not only maximizes heat transfer but also allows for easy maintenance and cleaning, which are critical considerations in industrial settings.
Key features of these exchangers include:
- Compact design, allowing for space-efficient installation
- High thermal conductivity due to the finned surface
- Flexibility in handling different types of fluids and temperatures
Such attributes make finned double pipe heat exchangers a preferred choice for industries looking to optimize their thermal processes.
Applications and Advantages
Finned double pipe heat exchangers are widely used across various industries due to their versatility and efficiency. In chemical processing plants, they facilitate the transfer of heat between chemical reactions, thereby maintaining optimal reaction conditions. In power generation, they are employed to recover waste heat, improving the overall efficiency of power plants. Moreover, in HVAC systems, these exchangers help regulate temperatures, ensuring energy-efficient climate control.
The advantages of using finned double pipe heat exchangers include:
- Improved heat transfer rates, leading to enhanced process efficiency
- Reduced energy consumption, contributing to cost savings
- Durability and long-term reliability, minimizing maintenance costs
Their ability to handle high-pressure and high-temperature fluids further accentuates their utility in demanding industrial environments.
Cost-Effectiveness and Reliability
Investing in finned double pipe heat exchangers can be a cost-effective decision for industries aiming to improve their thermal management systems. The initial investment is often offset by the long-term savings in energy costs and reduced maintenance expenses. The robust design of these exchangers ensures a long service life, which translates to fewer replacements and downtime.
Furthermore, the reliability of these exchangers is backed by their ability to operate under varying conditions without compromising performance. This reliability is crucial for industries where consistent thermal management is essential for operational success. The combination of cost-effectiveness and reliability makes finned double pipe heat exchangers a smart choice for any industrial application.
Conclusion: The Future of Thermal Management
As industries continue to seek ways to enhance efficiency and reduce operational costs, the role of finned double pipe heat exchangers becomes increasingly significant. Their design, efficiency, and reliability make them an integral part of modern thermal management systems. By investing in these exchangers, industries can ensure optimal performance, energy savings, and long-term sustainability. As technology advances, the potential for even more efficient designs and materials will likely expand the capabilities and applications of these vital components, securing their place in the future of industrial processes.